Table of Contents
- Protecting your heat exchanger
- Types of Service & Repair
- The Thermaline Difference
Protecting your Heat Exchanger
Heat exchangers play a crucial role in any production plant, whether you’re dealing with food processing, beverage, dairy, breweries, distilleries, bio pharma, or cannabis. No matter the industry you’re in, people depend on high-quality products from you. While it may not come to mind given how robust heat exchangers are, they require good upkeep and inspection.
As durable as they are, heat exchangers need those maintenance checkups to ensure they’re functioning optimally and efficiently. Without maintenance, heat exchangers can foul which could lead to an unplanned shutdown or failure–costing you thousands of dollars in wasted energy consumption, and disrupted operations.
We offer on-site services,inspections, preventive maintenance, and complete rebuild services to ensure that consistent efficiency for your processing needs.
In this post, we’ll cover some of the ways in which our maintenance and repair services can help your plant.
Types of Heat Exchanger Service & Repairs
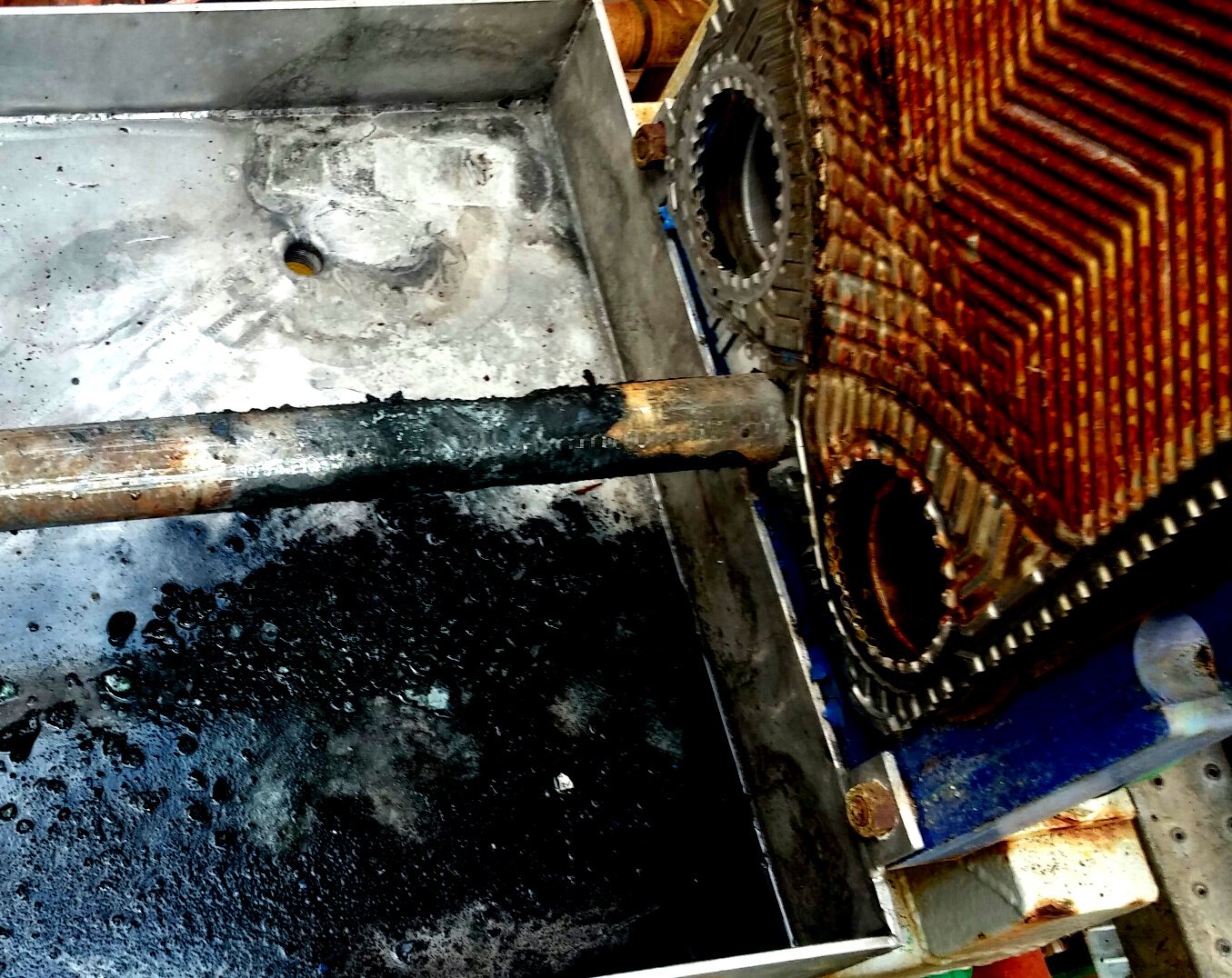
We provide various types of services for your heat exchanger, which can be done on-site or in-shop. All of our professional services minimize any downtime, and help ensure that your equipment continues to optimally perform.
Our in-shop services include:
- Plate pack refurbishment or replacement
- Re-gasketing
- Comprehensive plate cleaning services
- Frame refurbishment
- NDT Dye testing for cracks and defects
- Performance testing
- Entire unit refurbishment (sandblasting, repainting, assembly and hydro test of unit)
Learn more in our heat exchanger testing guide, and schedule heat exchanger CCT testing to ensure your heat exchanger keeps functioning at full capacity.
Our on-site services include:
- Plate pack installation
- Pressure washing
- Re-gasketing
- Equipment testing and maintenance
These services matter to address common issues including rust, fouling and deposits, which can negatively affect your equipment. Through regular maintenance, your unit will not only perform at its peak, but will also stay safe. Plate fouling can decrease your plant’s efficiency, and occasionally lead to product contamination. Our Thermaline plate rebuilding services can remove fouling and bring your equipment up to peak performance saving you money and energy by increasing heat transfer efficiency.
Plate Heat Exchanger Services
In terms of plate heat exchangers, we offer a wide range of gaskets and materials to fit most makes and models. Gaskets for our units can be purchased online through our parts store, or by contacting one of our application experts.
Our 9-part video series further explains about Maintaining Your Plate Heat Exchanger. In it, you can learn about gasket replacement, plate cleaning, and more. Our reconditioning center can bring your fouled or rusted plates back to their optimal condition.
We’re often asked how often gaskets should be changed. Gasket replacement will vary, as it depends on the product, process and temperatures. We recommend keeping 10% of the required quantity of gaskets on hand at all times in case of gasket failure. If multiple gaskets fail within a short period of time, then we recommend that all of the gaskets be replaced.
Tubular Heat Exchanger Services
We also offer services for tubular heat exchangers, including vacuum testing, tube sheet re-facing, tube plugging, pressurized integrity testing and Clean-In-Place (CIP) & Mechanical cleaning, which includes circulation of cleaning solutions to remove foulants and setting up a preventative maintenance schedule. CIP cleaning does not require disassembly of your heat exchanger.
When it comes to seal replacement, this also depends on the product and process. Just as PHE’s we recommend keeping 10% of the required quantity of seals on hand at all times, in case of seal failure. If multiple seals fail within a short time span, then it is recommended that all of the seals are replaced.
No matter what your needs are, our service technicians are happy to help with further product insights, or to provide repair/maintenance services. We can create a custom maintenance plan for your plant, based on your allocated budget.
Schedule service and testing, order spare parts or request a quote from our team.
What testing method do I use to check for leaks in my plate heat exchanger?
While dye testing can help come across internal leaks and cross contamination, it’s only one method of heat exchanger testing. This method requires each plate in your plate pack to be set out, sprayed on one side with dye and the other side sprayed with a developer. If you see dye leach through onto the developer side then that's where you know you have either a crack in the plate or pitting. Since it was introduced, the industry standards for testing have evolved. The FSA, USDA, 3-A and other regulatory agencies specify that a heat exchanger be tested using “a method capable of detecting an internal leak.”
Another method of testing includes using helium. This does not require you to disassemble your heat exchanger. The helium is inserted into one side of the system while a helium reader is used on the other side. If helium is detected on the opposite side of the plates, then you know you have a leak. Although this is known to be an accurate style of testing, this practice proves to be very costly, especially when put to use in large systems, requiring large amounts of helium.
Our patented CCT(cross-contaminated tester) program is setting new standards in the way heat exchanger testing is performed. Our test is both comprehensive and cost effective with a program that fits your custom testing needs, pinpointing the problem within minutes. Dye testing alone is a tried and true method but can be very time-consuming, messy and requires a trained technician to interpret test results thoroughly.
Proper Disassembly of your heat exchanger
Heat exchanger maintenance requires that your heat exchanger is currently shut down–including with valves turned off from all fluids.
Prior to service, you’ll want to follow your company’s lockout procedures as needed to ensure all fluids are properly drained. You’ll also want to allow the unit to fully cool down, and relieve all pressure on the heat exchanger, before you begin.
If you’re worried or unsure about disassembly processes, or would prefer to get additional assistance, you can reach out to us and schedule an on-site visit for maintenance.
The Thermaline Difference
For nearly three decades, our Thermaline team has manufactured innovative heat transfer solutions made in the USA–and distributed all over the world.
Since we operate as a small, nimble team, this allows us to tailor every product to your specific needs. Our proprietary online product system also lets you customize your designs, receive a quote, and instantly purchase in-stock equipment directly from us.
We are the industry standard in heat exchanger engineering, and are certified by 3-A and ASME. We build all our products to meet stringent consumer safety standards and energy consciousness.